Daan technologie is a start-up that was created in 2016 by Damian PY and Antoine FICHET in order to unite around the creation of Bob. “We created Daan Tech in 2016, in fact, to launch Bob the mini dishwasher. I wanted to start a hardware business that was more robotics/energy oriented, and Antoine had come up with this idea for a mini dishwasher, so I thought it was a good idea to start with.” confides Mr. PY.
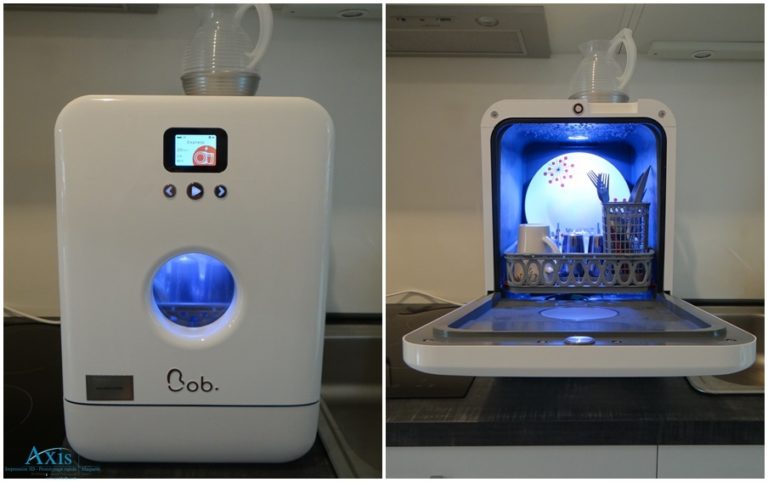
Axis has been manufacturing 3D printed prototypes for over 20 years.
Helping to create the BOB model was not a challenge for us. Our know-how enabled us to test the different versions of BOB and validate the parts using HP Multijet Fusion and Stereolithography.
The creators of the ultra-compact dishwasher began by creating their prototype in various materials that had nothing to do with 3D printing, as the first step was to create a thermoforming mock-up. Daan technologies then went on to equip itself with a wire-dispensing 3D printing machine to produce more complex shapes: “We then developed the Bob v5, which we had made at Axis in the summer of 2018 and with which we succeeded in our pre-orders. This prototype is really at the root of our success, we took the first photos of Bob in Berlin, at the EIC Summit, we then launched pre-orders, we won the Blue Ocean award with it, and then it ended its life after a makeover at CES Las Vegas 2019. “
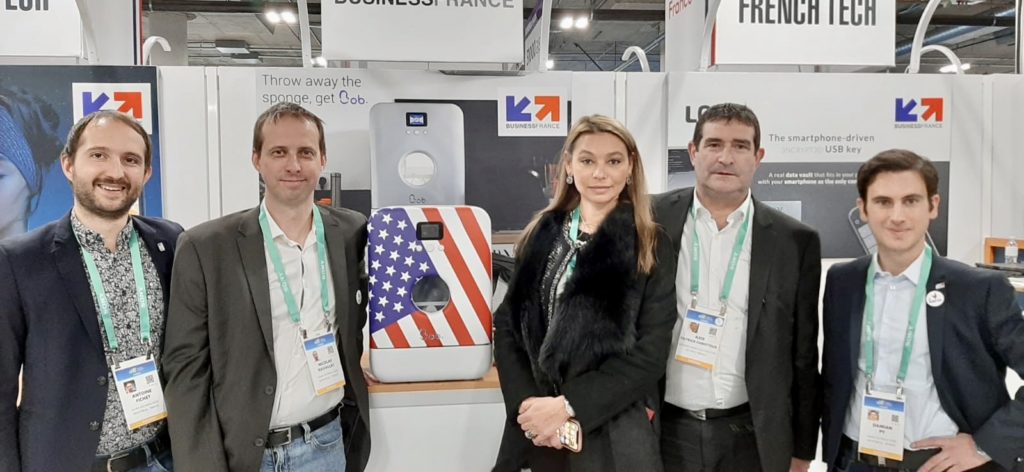
Axis has been a specialist in additive manufacturing rapid prototyping since 1997, so it was a no-brainer for us to help Daan Technologies when they called on us to produce a realistic mock-up of the final product. “We wanted to produce a prototype that would be faithful to the final product, with exactly the same dimensions, and that would enable us to validate the parts before launching the molds. “says Damian Py.
So we produced parts using powder sintering as well as stereolithography, to give this start-up the possibility of having a finished product very close to what Bob would produce after injection molding.
As the co-founder explains, “Rapid prototyping not only enabled us to validate the technical functioning of the product, but also to have a product to show our customers and investors. Without these rapid prototyping tools, it would have been impossible for us to succeed with our pre-order campaign or convince investors.”
In fact, stereolithography was chosen to produce the outer parts of the prototypes, i.e. those where aesthetics were most important. This 3D printing technique makes it easy to produce smooth parts that can be finished with paint and primer. This additive manufacturing technique is often favored for validating parts, especially from the point of view of overall appearance, as it enables us to obtain parts that are fairly close to the final products that will be launched on the market.
Powder sintering was used to prototype the interior of the dishwasher. Thanks to the sintering of PA 12 powder and epoxy impregnation, it was possible to test the effectiveness of the product itself, as well as its final appearance. Powder sintering is a favored material for parts requiring good mechanical performance. The granular/porous aspect of sintered powder is more difficult to finish aesthetically, which explains the different materials used in Bob’s production. In addition to the dishwasher model, we were also involved in the production of BoB’s “options”. In fact, it’s not just a dishwasher: with the addition of a module, Bob can also become an ally in the UV-C disinfection of your masks and other objects. Very practical in these times!
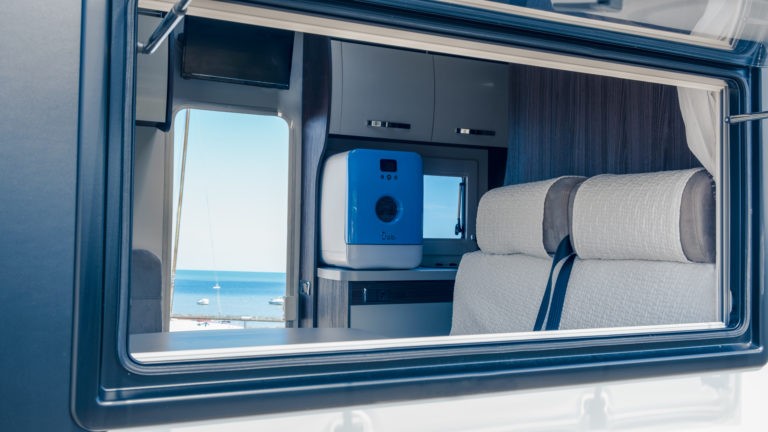
We wish Daan Technologies all the best for the future as they continue their adventures: “Firstly, adapting Bob to international markets, particularly in Asia (Japan, China, Hong Kong, Singapore, Taiwan, South Korea). Secondly, the development of an autonomous washing machine (we’ve just received confirmation from the BPI that we can begin development). Finally, the development of a Bob XL, 6 place settings with water saver (same water consumption as Bob, more powerful UV), aimed at the North American market and households larger than Bob (we are awaiting confirmation from Europe)”, says Mr Py.
Our company is delighted to have been able to participate in this fine Made In France project, 100% of which is produced in France. We’re waiting to receive our Bob so that we can fully test its effectiveness in all areas.