Before the advent of 3D printing, the launch of a new product necessarily involved making a mold for a few dozen parts, or even a single prototype. Today, more and more companies are turning to additive manufacturing to gain in flexibility and time for production runs of up to a few thousand parts. Axis has been offering this service since 2017, and requests continue to grow, proving the market’s interest in this new production method.
Faster time to market
It takes between 2 and 4 months to make an industrial production mold using traditional methods. The price also depends on the size and the modifications to be made during the process. In an increasingly competitive market, these delays and costs can be an obstacle to the success of the product, or even the company if it’s a start-up.
3D printing makes it possible to produce a finished product in just a few weeks, and to test the market while waiting for the final mold if necessary. This responsiveness is perfectly suited to start-ups, the events market (trophies, goodies, customer gifts…) or major brands that are increasingly launching limited edition products or ultra-customized projects (see our article on the mini series for Louboutin).
3D-printed mini-series are also suitable for emergencies. At the start of the Covid crisis, axis teams mobilized to produce visors, tracheal valves and ventilators in epoxy resin or on our HP Multijet fusion (see our article on this subject).
We often imagine that 3D printing is limited to prototyping, because the part produced would not resemble the finished product, or would not have all the desired technical or mechanical characteristics. This image is, in fact, totally outdated, as the variety of materials (plastics or metals) available for 3D printing continues to grow, and already covers most industrial needs. At Axis, the multitude of technologies and materials we use enables us to meet the most specific requirements. FDM, SLA, SLS, MJF HP and vacuum casting enable mini-series production of up to 10,000 parts, more than enough to cover the first few months of product sales. Finishing with paint, varnish or heat treatment then gives the final look and all the characteristics expected by our customers.
So if you too would like to launch a production project, contact us so that together we can define the technology that is right for you.
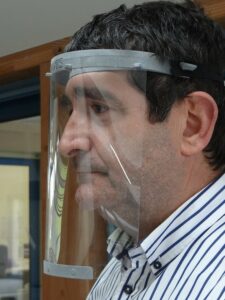