Trotz unsicherer wirtschaftlicher Zeiten investiert Axis weiter, um der steigenden Nachfrage seiner Kunden gerecht zu werden. Die Wahl fiel natürlich auf eine neue RAPLAS 700, die die im letzten Jahr erworbene erste Maschine unterstützt (lesen Sie den Artikel).
Patrick Christoux, Präsident der Firma Axis, erklärt: „Nach einem Jahr mit dem RAPLAS 700 konnten wir uns ein Urteil über die Druckqualität der Maschine sowie über ihre Geschwindigkeit bilden. Das von uns verwendete Harz ermöglicht die Herstellung präziser Teile mit hervorragenden mechanischen Eigenschaften, und die variable Dimensionierung des Strahls führt zu einer Oberflächenbeschaffenheit von höchster Qualität. Unsere Kunden wissen das zu schätzen und sagen uns das, indem sie ihre Teile auf dieser Maschine weiterempfehlen.
Um der steigenden Nachfrage gerecht zu werden, war es für uns selbstverständlich, in die gleiche Technologie und die gleiche Marke zu investieren.
Auch wenn RAPLAS ein „offenes“ Harzsystem anbietet, das es ermöglicht, nicht durch die Harze des Herstellers eingeschränkt zu werden, verwenden wir hauptsächlich ihr weißes ABS-Harz , das jedes Mal unsere Spezifikationen erfüllt und REACH-konform ist und den ROHS-Standards entspricht.“
Wenn Sie mehr über unser neuestes Gerät erfahren möchten und was es Ihnen bringen könnte, kontaktieren Sie uns bitte über das Kontaktformular oder direkt über unsere Beratungs-E-Mail-Adresse axis@axishello.com.
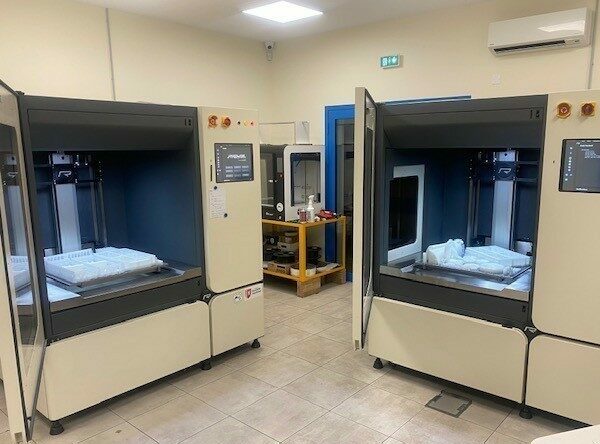
Mehr über ALS :
DIE RAPLAS 700 verwendet die additive Fertigungstechnologie SLA. Der Begriff SLA kommt von StereoLithography Apparatus. Es handelt sich dabei um die älteste moderne additive Fertigungsmethode. Es ist übrigens diese Technologie, die den Dateien ihren Namen gegeben hat STL für STereoLithography. Das Konzept beruht auf der Herstellung eines dreidimensionalen Objekts durch Polymerisation mithilfe eines UV-Lasers. Ein lichtempfindliches Harz wird Schicht für Schicht durch die Bewegungen des UV-Lasers polymerisiert, der wiederum durch die zuvor erstellte Modellierung gesteuert wird (3D-Datei). Die Platte senkt sich allmählich ab, damit das Harz die vorherige Schicht überdecken kann. Wenn das Teil vollständig ausgehärtet ist, fährt die Platte wieder nach oben und man nimmt das Teil wieder auf.
Seine anschließende Platte mit den Maßen 700x700x500mm ermöglicht das Bedrucken von großen Teilen, die dank des dafür vorgesehenen Platzes leicht zugänglich sind. Zeitersparnis und Einfachheit beim Reinigen der Teile nach dem Drucken also.
Den aufmerksamsten unter Ihnen wird sicherlich der Stratéo des französischen Unternehmens e-motion Tech aufgefallen sein, ein 3D-Drucker, der auf der FDM-Technologie basiert. Weitere Informationen zu dieser Technologie finden Sie auf unserer Seite FDM-Drahtabscheidung und lesen Sie den Artikel über unsere Investition erneut.